Nitrous oxides (NOx) are formed by combustion in high-temperature environments, such as power plants and large diesel engines. NOx causes air pollution by reacting with air in UV light from sunlight to form ozone, the primary component of smog. Therefore, it is crucial to limit NOx emissions in applications that produce large quantities of these gases.
In both selective catalytic reduction (SCR) and selective non-catalytic reduction (SNCR), spray nozzles are used to inject a reagent or series of reagents into the exhaust gas to combine and react with the gas (and potentially a catalyst) to remove NOx from emissions. SCR uses ammonia as the reagent, while SNCR uses ammonia or urea injected at a high temperature.
BETE spray nozzles maximize efficiency in SCR/SNCR injection applications. They atomize and distribute the reagent into the process stream, which increases the reaction surface area that combines and reacts with the NOx. Spray nozzles coupled with BETE injection lances can distribute the reagents as evenly as possible within the process stream to ensure proper mixing and minimize bypass.
Common Uses & Industries
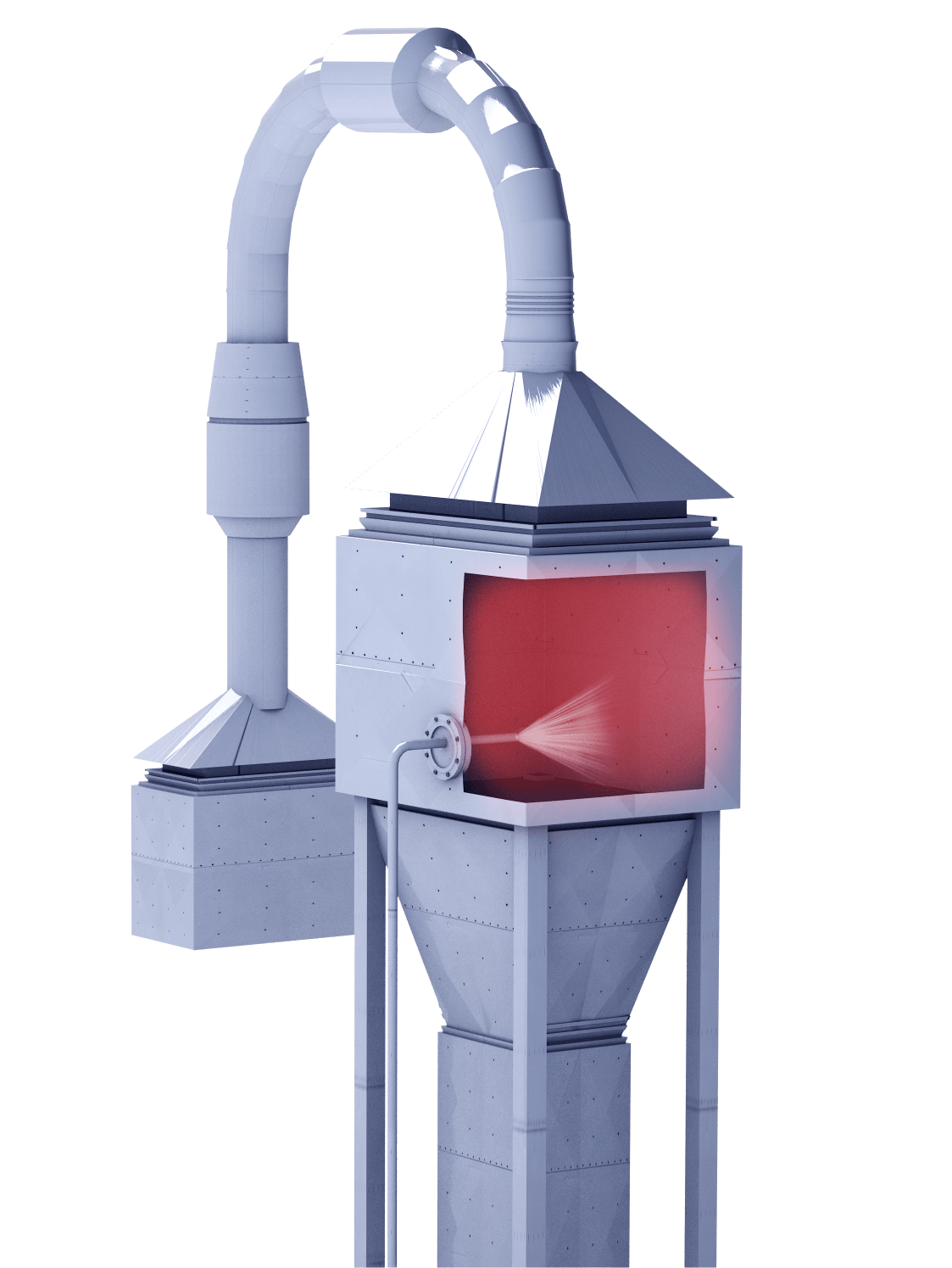
Important factors to consider:
Temperature and particulate content of a gas stream
- SCR/SNCR applications typically occur at high temperatures
- Particulate in the gas stream has the potential to clog injection nozzles and catalysts
- Injection lances may need to be designed to prevent flashing of the spray media before the nozzles or with protective / purge shrouds to prevent a build-up
Process gas flow rates and velocities
Scrubbing fluid composition
- Typically aqueous ammonia, anhydrous ammonia, or urea
Nozzle material of construction for high temperature and corrosive environments
Available nozzle mounting locations and distance to catalyst
- Nozzle arrangement is important to cover the flue gas and prevent bypass
- Proper residence time is required to ensure mixing and vaporization of reagents
Available pressure drop (∆P) across the nozzle
- ∆P = supply pressure at nozzle inlet – process pressure outside nozzle
- Availability of compressed air, nitrogen, or other carriers/atomization gases