TANK CLEANING NOZZLES
Large Selection in Stock & Ready to Ship
CLEAN TANKS FASTER, SAFER, & MORE EFFICIENTLY WITH BETE SPRAY TECHNOLOGY
BETE tank cleaning nozzles are engineered to improve cleaning tanks and equipment while reducing time, water, and labor costs. Our advanced spray technology ensures optimal coverage and maximizes cleaning impact by efficiently using the system’s available flow rate and pressure. Compared to traditional spray balls and cleaning methods like “fill and drain” or manual entry, especially in hazardous environments, BETE tank washing nozzles offer significant time and cost savings.
Our tank cleaning nozzles use the latest spray technology to optimize industrial or hygienic tank and equipment cleaning applications. We offer a comprehensive line of tank cleaning solutions for everything from light rinsing to removing stubborn residues – many options in stock and ready to ship.
Find Your Tank Cleaning Nozzle by Tank Size

HydroWhirl® Orbitor

HydroWhirl® Orbitor 100

HydroWhirl® Orbitor 100 XC
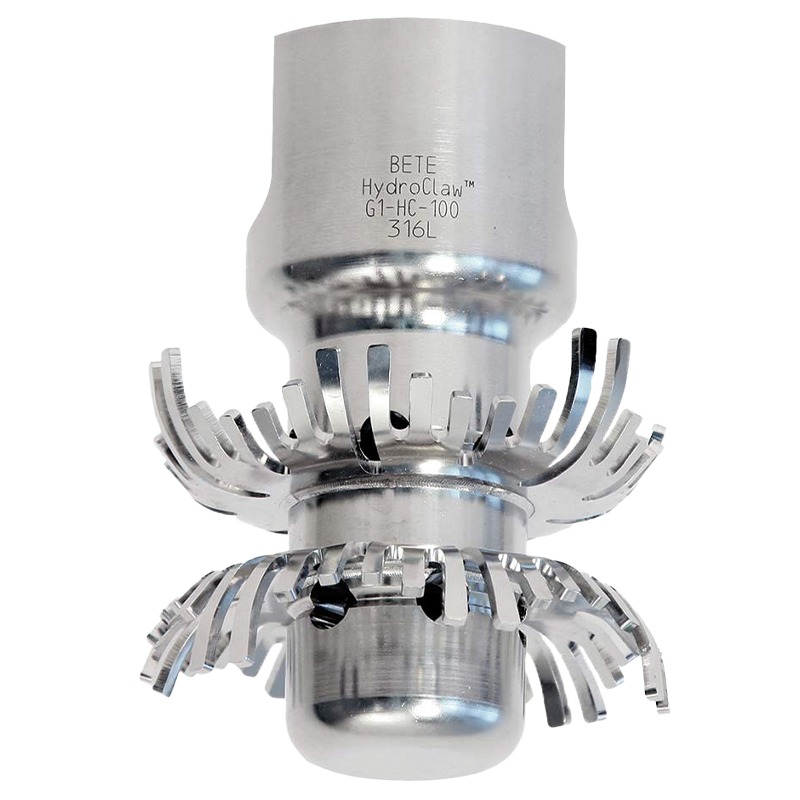
HydroClaw®
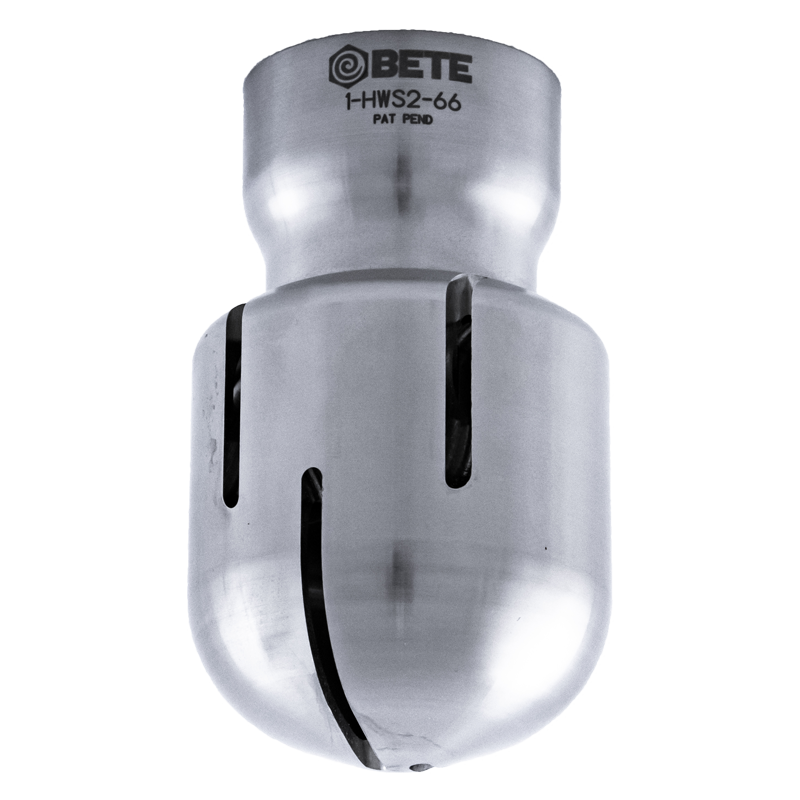
HydroWhirl® Stinger

HydroWhirl® Poseidon

HydroWhirl® Mini SS

HydroWhirl® Mini PVDF
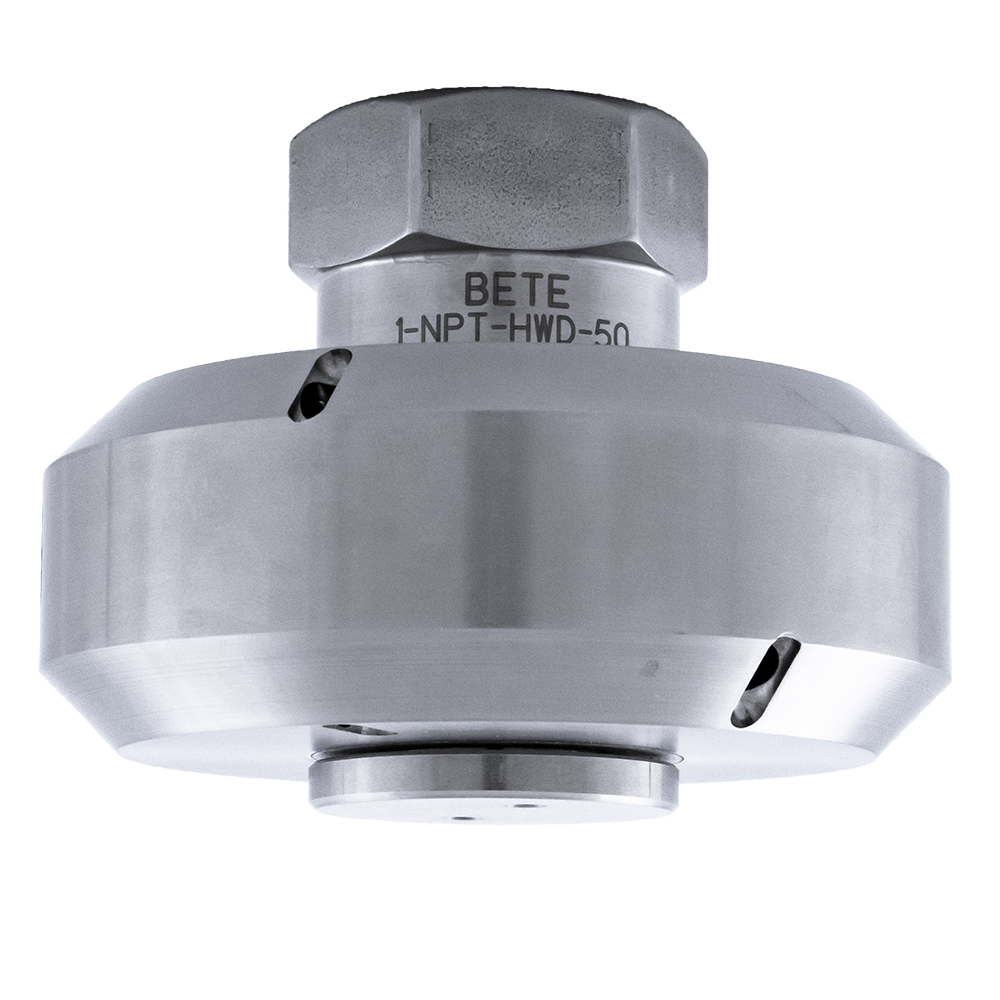
HydroWhirl® Disc (HWD)

TW
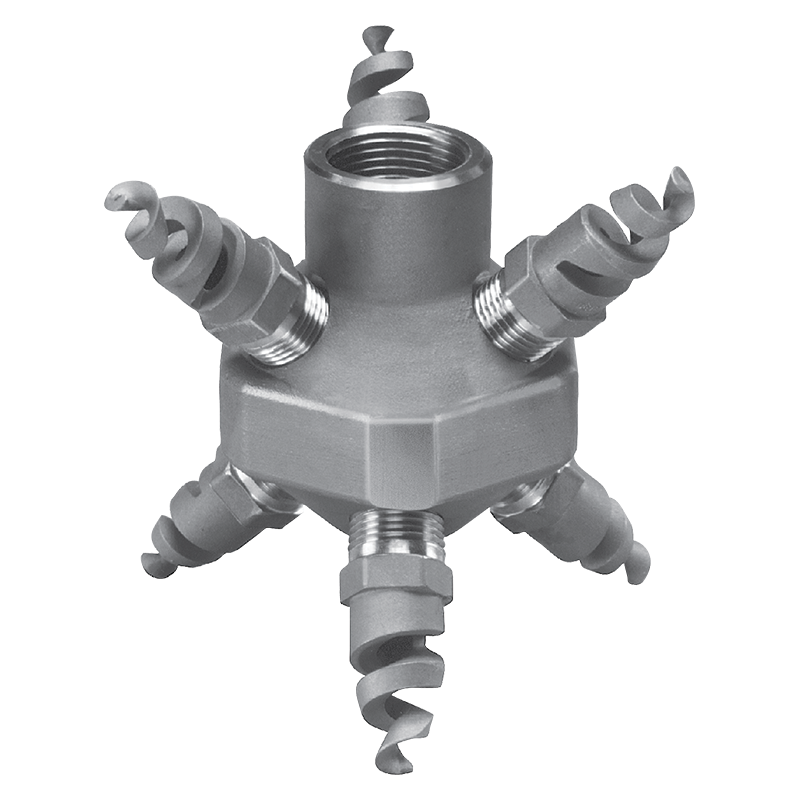
LEM

Clump
Common Uses & Industries
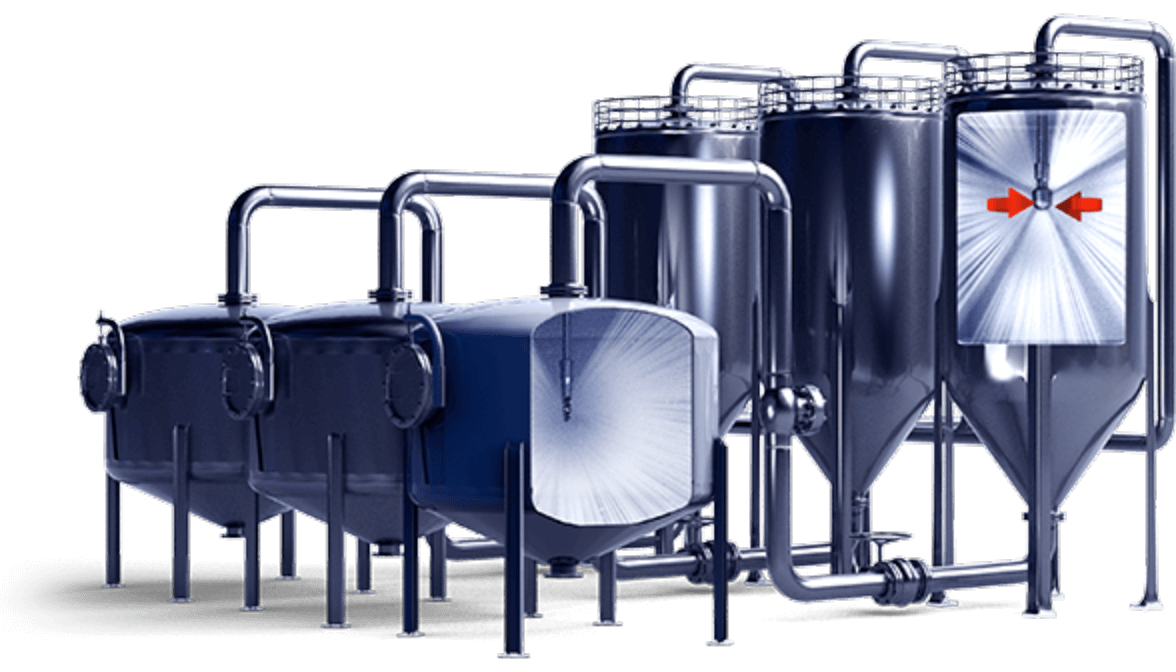
Related Tank Cleaning Solutions
Read Our Case Studies
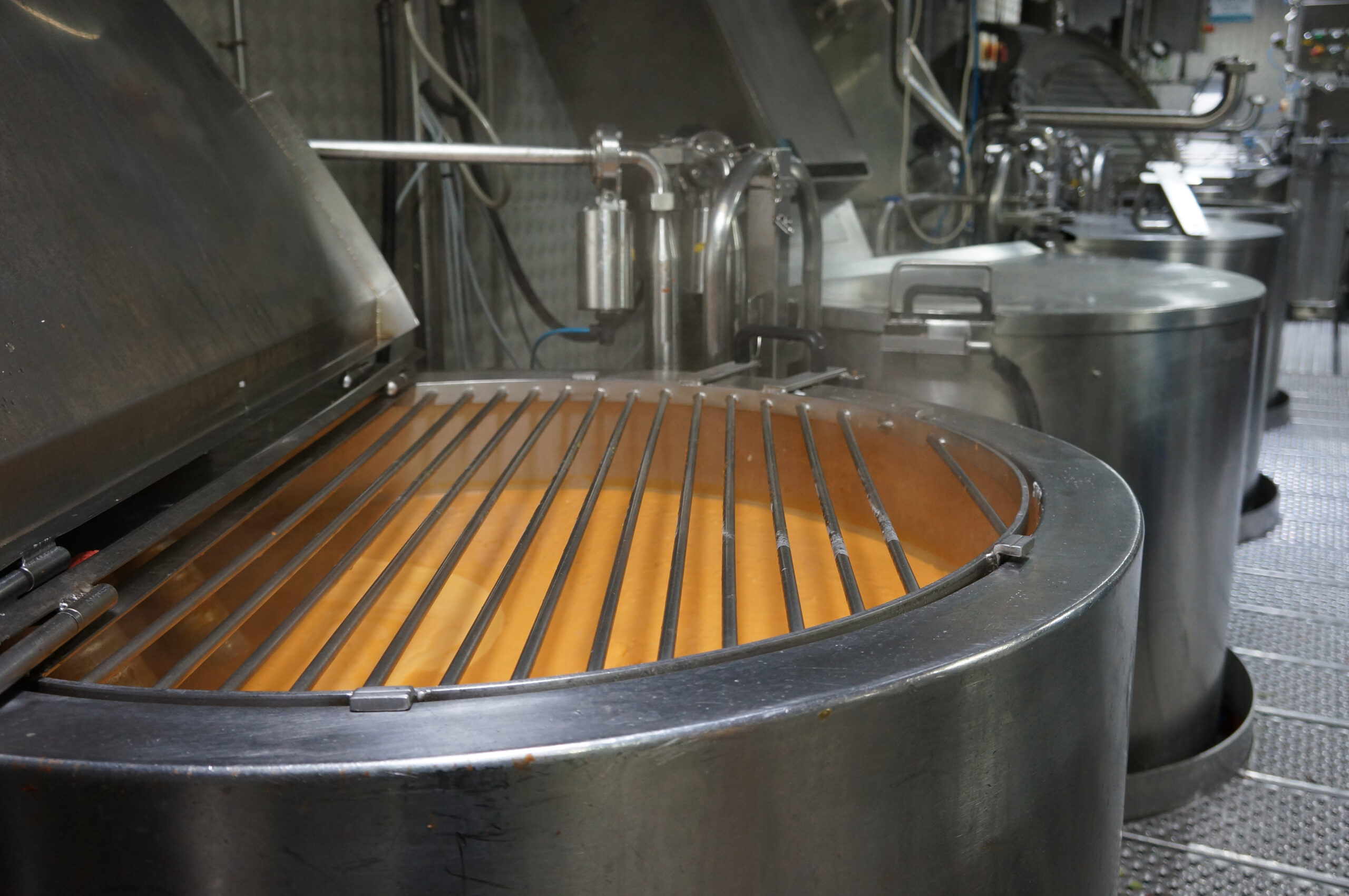
Tank Cleaning Nozzles Save Food Processor $96K Annually in Reduced Maintenance

HydroClaw® Improves Tank Cleaning Efficiency and Resolves Maintenance Issues for Tomato Processor
